Length Tolerance at Samson
In order to meet Samson quality standards and practices, all high-performance products made in whole or in part from high-modulus fibers such as HMPE, aramid, liquid crystal polymer (LCP), etc., are measured with a length tolerance of +5%/−0%. Other ropes made with olefin, nylon, or polyester fibers are measured with a length tolerance of +/−5%. These are determined during the reeling process, as described below.
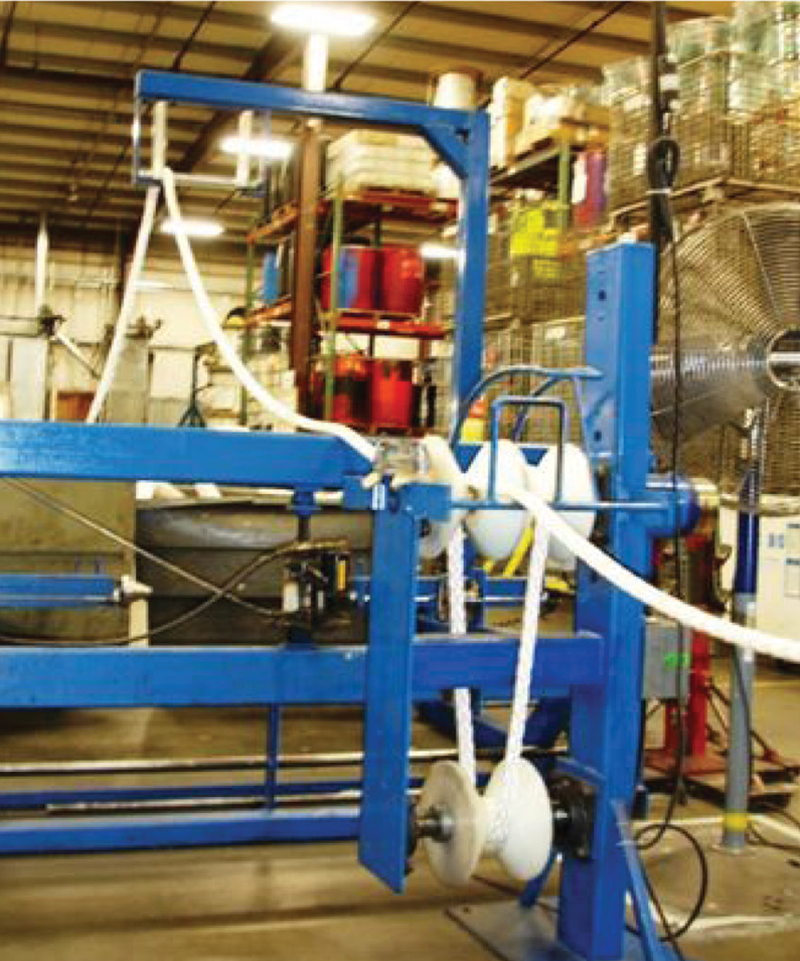
A rope is run over an elevated roller, or through two horizontal breaker bars that add back-tension to control the rope as it is pulled through the reeling system. The rope is then looped around a number of capstans that are controlled to a tension of 10 lb. The rope finally passes through a length counter as it is wound on to the final reel and cut at the required length. The back-tension on the rope as it moves through the counter assists in providing a consistent length measurement and a solidly wound reel.